Electric Actuator (Economical) FQ
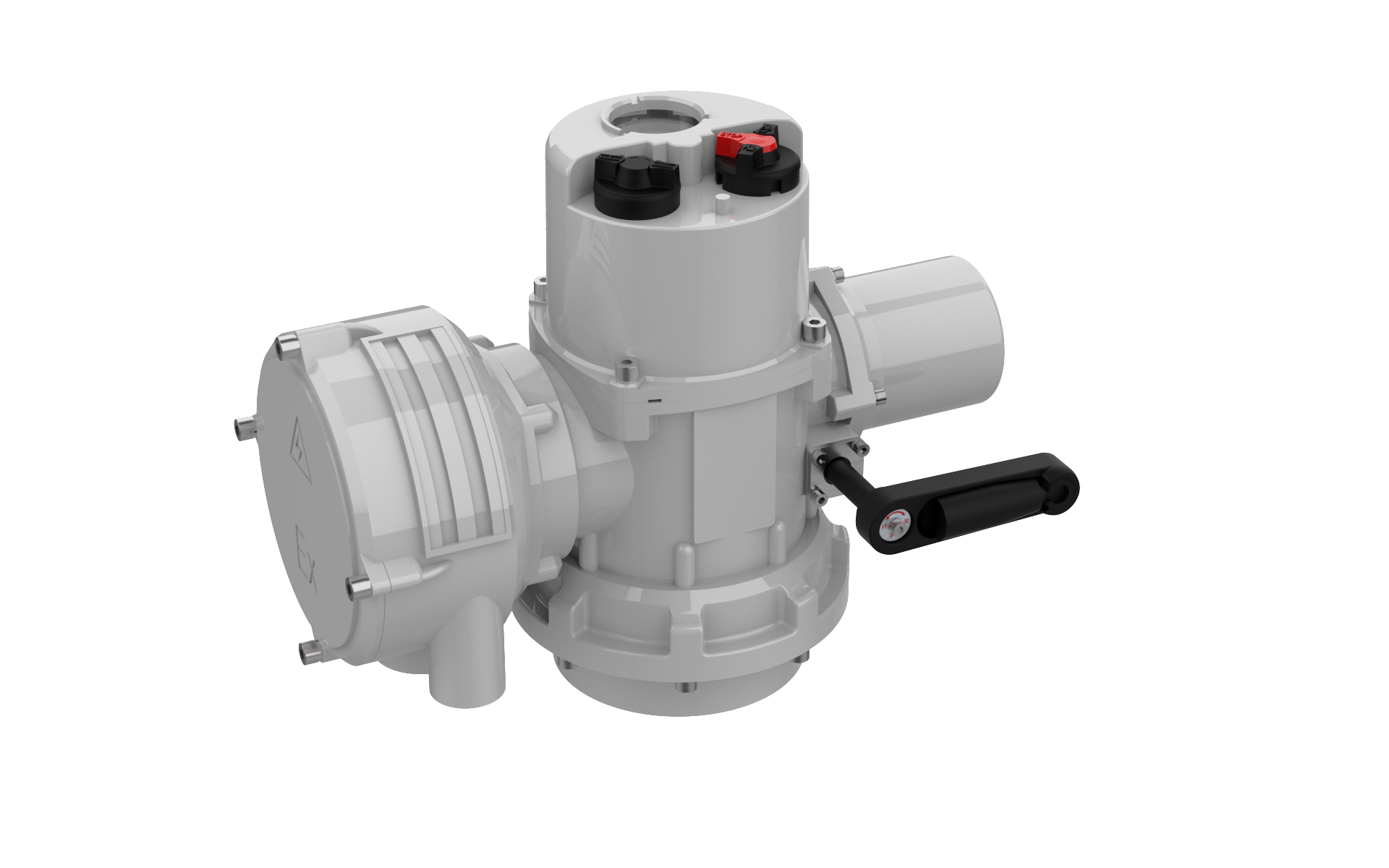
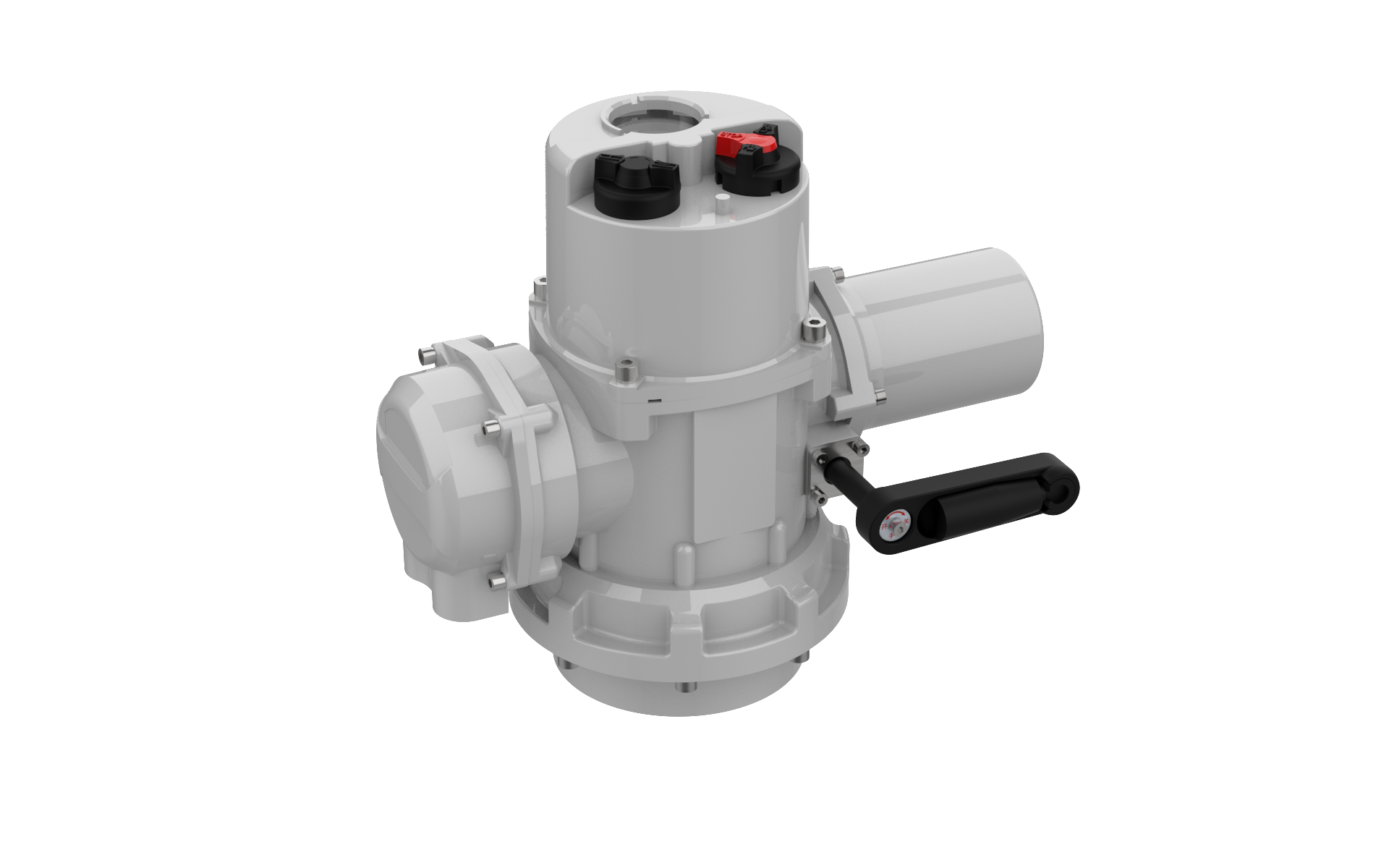
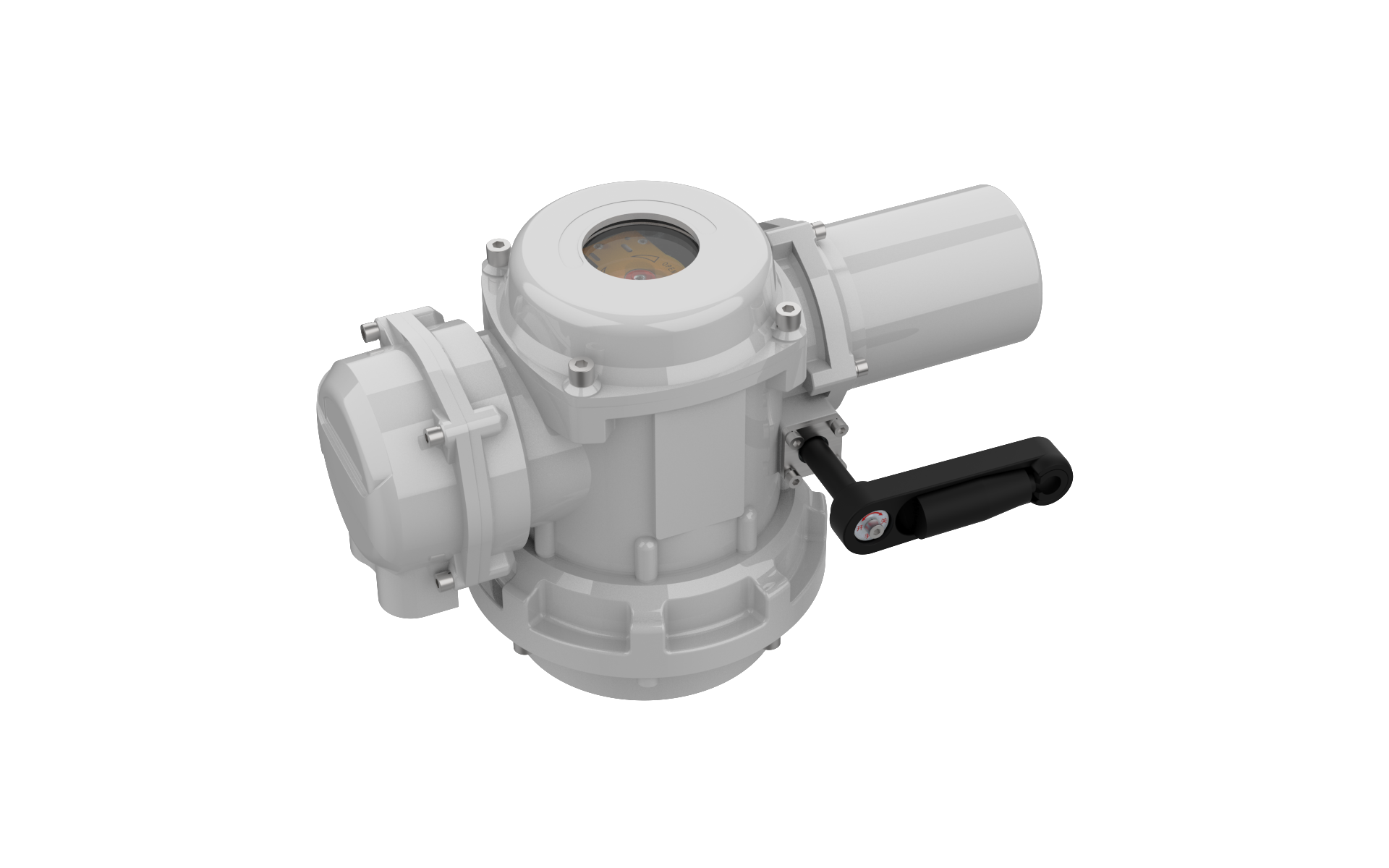
FQ Series is economical electric actuator.
Quarter-turn : 100 – 30000Nm
Linear Travel : 1 – 120KN
I. F/FQ economical series
Standard Configuration Technical Parameters | |
Basic Parameters | AC Motor |
Product Series | F/FQ Series |
Power Supply | 230/400/660VAC ±10% 50/60Hz |
Torque / Thrust | Part-turn: 40,000-300,000Nm |
Speed Range | × |
Torque Range | × |
Torque Detection | Detecting changes in motor operating current |
Torque Detection Accuracy | ±5% |
LCD/OLCD | 4 lines display, English and Chinese switching |
Position Sensor | Absolute encoder |
Input / Output | Analog quantity: 4-20mA / 4-20mA; Switching quantity: dry contact; Wireless remote control ( 1-10Km ) |
Control Accuracy | ±0.8 % |
Receive Command Response Rime | 100ms |
Motor Commutation | AC contactor |
Motor Commutation Time Interval | Stop ( need stop ) |
Motor Overshoot | Large overshoot |
Motor Load Rate | working state S2 100% 15min working state S4 100% 600c/h |
Ambient Temperature | -25-70℃ or -60-60℃ |
Environment Humidity | 95%RH |
Protection Level | IP67 |
Explosion-proof Grade | Ex dⅡ B T4/5 |
Communication Protocol | ModBUS-RTU ProfiBUS-dP HART |
Set Alarm | 5-way relay alarm output |
Seismic Performance | Manufacturer test standard: at 600Hz 3 axis direction 10g state, it continuous successfully worked 180 days. |
Split Installation | Split Control Box: The local display, operating panel, controller, etc., are placed at a location ≤40m away. Actuator Body: The motor, position sensor, etc., are fixed in the host body cavity in a special way. Split installationdistance≤40m |
Solar Power | Solar power supply in the field without power supply |
II. Application
Suitable for severe working conditions with ultra-high torque requirements and maintenance-free environments.
III. Features
- At the allowable range of torque and speed conditions, it can replace electric-hydraulic or pneumatic-hydraulic actuators;
- Offering economic practicality.
- Requiring minimal maintenance.
IV. Purchase Guide
When choosing the actuators, customers should select suitable models based on information such as valve torque, working conditions, and valve size. It is recommended that when choosing an electric actuator model, 60% – 80% of the rated output torque of the actuator should be used as the working torque of the valve. If the application scenario is very important or the environment is complex, customers should provide design drawings and detailed parameters as much as possible for the company’s experts to review and recommend matching products.
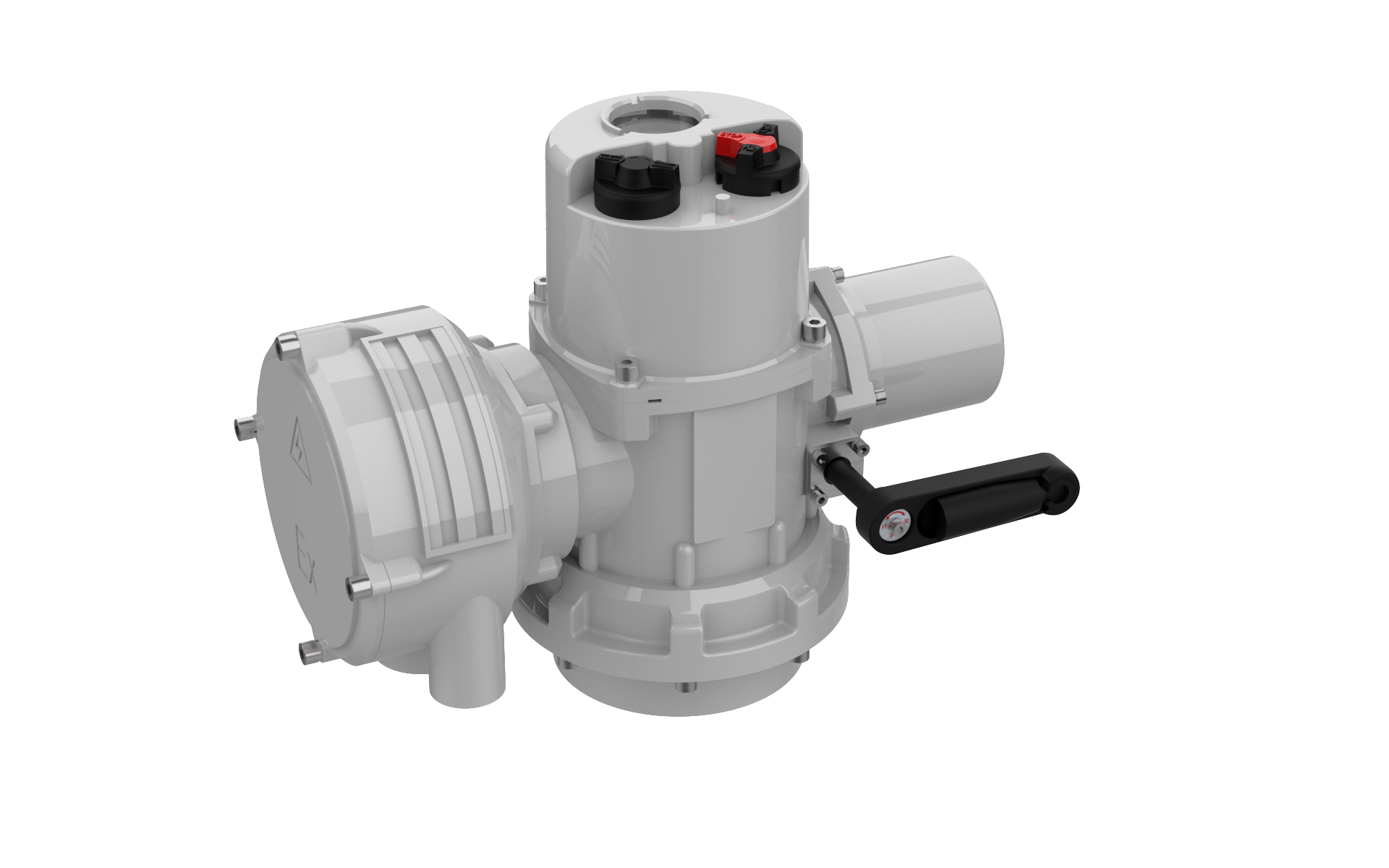