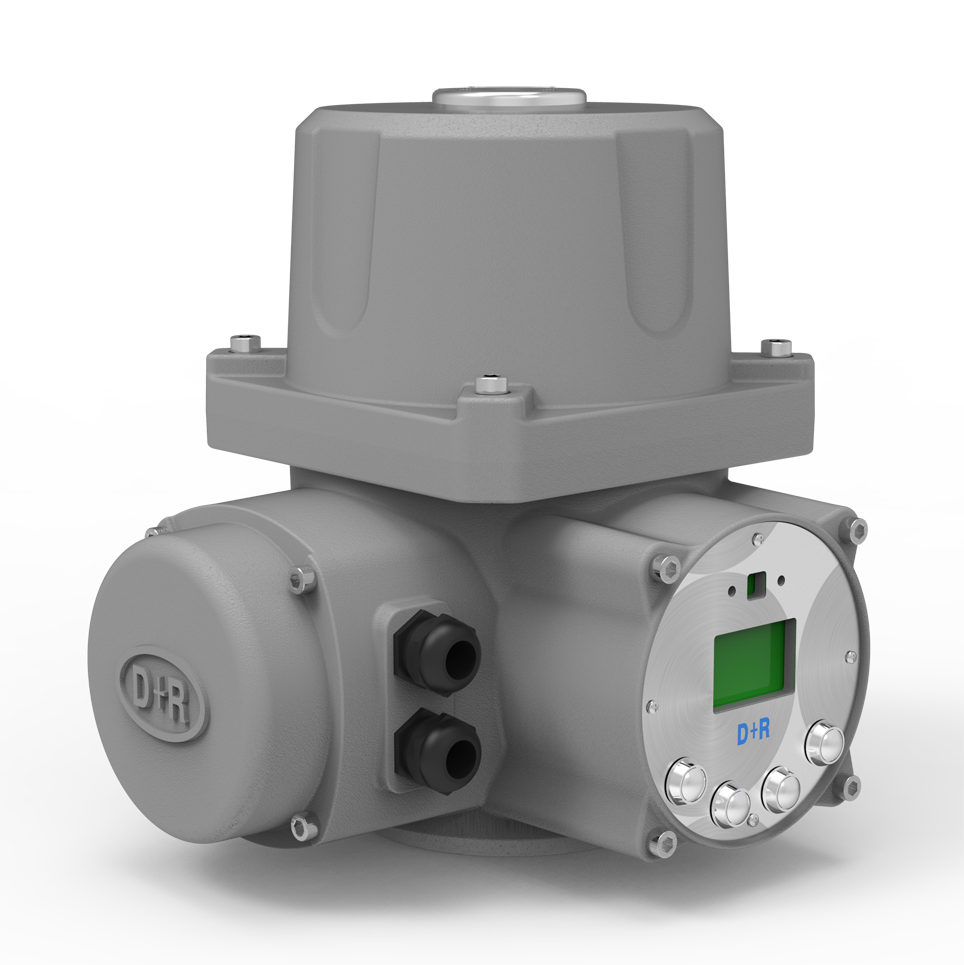
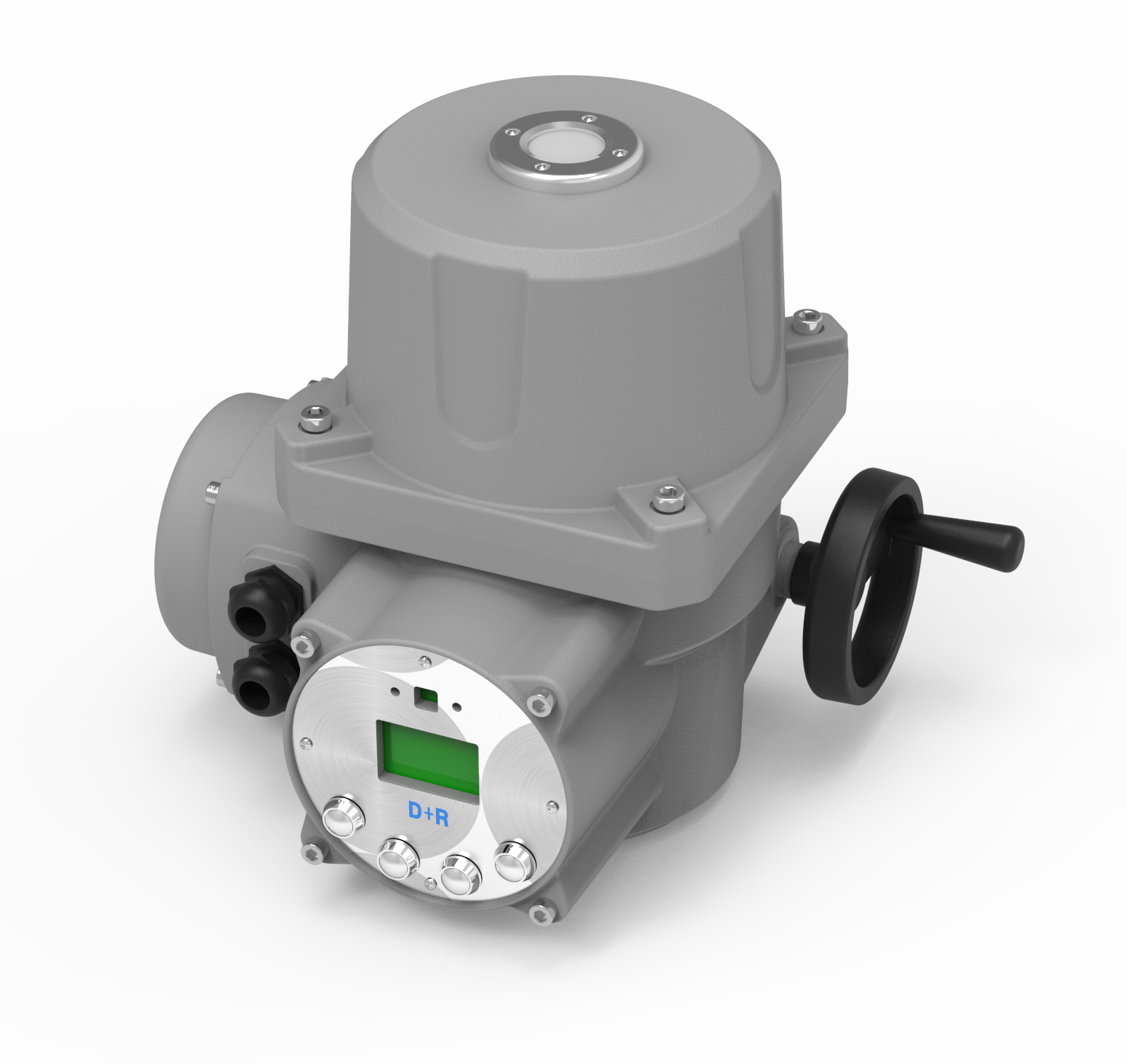
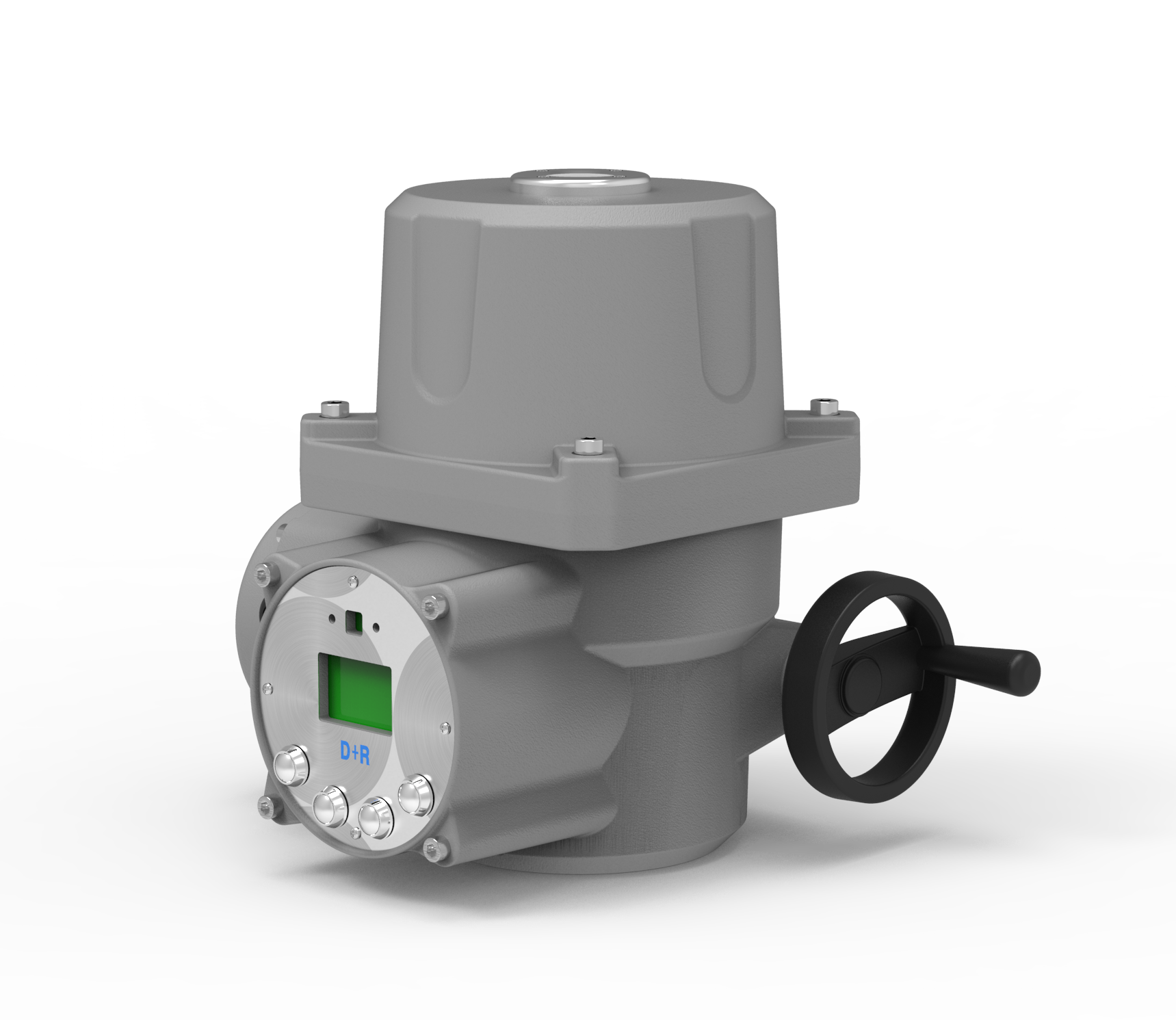
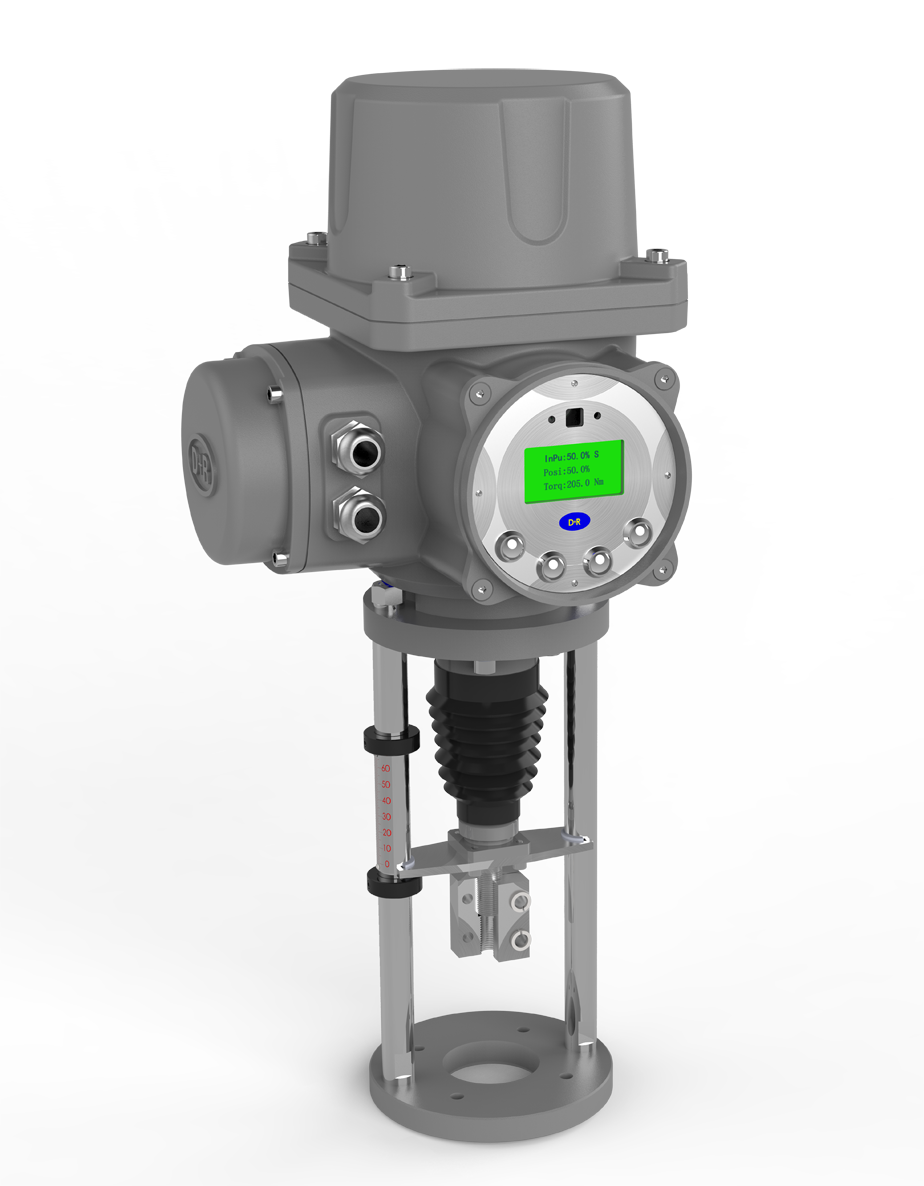
G 1 & G 2 : Permanent magnet DC brushless speed control electric actuator is suitable for high-precision, high-speed, frequent start-up, and harsh working conditions.
Quarter Turn : 100Nm-300,000Nm,
Linear Travel : 1KN-120KN.
I. G 1 & G 2
It’s based on different motor power, gear ratios, output shafts, and output flanges, determines the torque output of the actuators. The torque output range for multi-turn actuators is 30-15000Nm, with a maximum output speed of ≤127rpm.
The G series products use permanent magnet brushless DC speed-regulating motors, planetary gear structures, and top-tier industrial electronic components.
Standard Configuration Technical Parameters | |
Basic Parameters | BLDC Motor |
Product Series | G series (Hiah speed /precision,full function) Ball / Butterfly / Contralvalve |
Power Supply | 12/24/36/48/72VDC ±2% 110/230/400/600VAC ±25% Solar+DC electric actuator |
Torque / Thrust | Part-turn: 100-300000Nm Linear: 1-120KN |
Speed Range | 15%-100% ( rated motor speed ) |
Torque Range | 2-3 times standard torque (not all of them can reach 3 times torque) |
Torque Detection | Detecting the current changes during the motor operation |
Torque Detection Accuracy | ±3% |
LCD / OLCD | 4 lines display, English and Chinese switching |
Position Sensor | Absolute encoder |
Input / Output | Analog quantity: 4-20mA / 4-20mA; Switching quantity: dry contact; Wireless remote control ( 1-10Km ) |
Control Accuracy | ±0.1%, For high precision control, Have to use DAUME provid valve. |
Receive Command Response Rime | 50ms |
Motor Commutation | Electronic commutation |
Motor Commutation Time Interval | Immediately ( no need stop ) |
Motor Overshoot | No overshoot or slight overshoot |
Motor Load Rate | Load ratio 300%, working state S5 Start frequency is not limited |
Ambient Temperature | ‘-40-85℃ ( convention ) ‘-60-60℃(mention in the order) |
Environment Humidity | 100%RH |
Protection Level | IP69 Underwater 12m normally working |
Explosion-proof Grade | Ex dⅡ C T5 |
Communication Protocol | ModBUS-RTU (std) ProfiBUS-dP HART |
Set Alarm | 6-way relay alarm output |
Seismic Performance | Manufacturer test standard: at 600Hz 3 axis direction 10g state, it continuous successfully worked 180 days. |
Split Installation | Split Control Box: The local display, operating panel, controller, etc., are placed at a location ≤40m away. Actuator Body: The motor, position sensor, etc., are fixed in the host body cavity in a special way. Split installationdistance≤40m |
Solar Power | Solar power supply in the field without power supply |
II. Key Features
- Non-intrusive Design: No need to open the cover; parameters can be set through panel buttons or remote control for convenient operation.
- Rich Display Functions: Clearly displays valve position, sensor location, etc., making it intuitive and easy to understand, replacing traditional symbol codes.
- Efficient Mechanical Transmission: Uses NGWN-II transmission principle with high efficiency, strong load-bearing capacity, and long life.
- Adjustable Motor Speed: Achieves DC speed regulation to protect valves from liquid erosion.
- Adjustable Torque: Torque can be reset via the panel or remote control, with a range of F1SF2.
- Avoidance of Water Hammer and Cavitation: The entire stroke can be divided into three segments for setting, following the valve’s flow characteristic curve.
- Electronic Stroke Limiting: Simple and reliable operation, easily completing stroke settings through jogging or manual operation.
- Strong Interference Self-recovery: In case of signal interference causing a system crash, the system automatically recovers to the state before the crash.
- No Clutch Handwheel Mechanism: The handwheel can be turned at any time, and the actuator automatically returns to the position indicated by the last received signal.
- Local/Remote Switching: One-button switching between local and remote operations.
- Timely Protection Functions: Equipped with various protection functions and automatic sequence recognition.
- Over-torque Protection: Two levels of protection are provided; level one is for normal operating torque, and level two is the maximum safety value for equipment protection.
- Unjamming Function: Automatically attempts three reciprocating impacts; if the jam is cleared, it continues running; otherwise, an alarm is triggered.
- Start Frequency: Brushless DC motors ensure that the actuator can immediately change direction without damaging the motor.
- Frictionless Electronic Measurement Technology: Achieves precise valve position control without overshooting.
- Modular Design: Independent unit design facilitates maintenance and upgrades.
- ESD Function: Prioritizes ESD function control in emergency situations.
- Separate Installation: Suitable for high-temperature, narrow-space, and severe vibration environments.
- Fieldbus (Optional): Modular circuit design allows for the addition of ModBUS, ProfiBUS-dp, HART functions.
- Supports 4G and Wireless Remote Control: Suitable for outdoor environments.
- Solar Power Supply and Wireless Signal Transmission for Power-free Areas: Supports solar power supply and wireless signal transmission in areas without electricity.
- Energy Saving and Environmental Protection: Compared to AC motors of the same power, it can save 40-50% energy.
III. Purchase Guide
When choosing the actuators, customers should select suitable models based on information such as valve torque, working conditions, and valve size. It is recommended that when choosing an electric actuator model, 60% – 80% of the rated output torque of the actuator should be used as the working torque of the valve. If the application scenario is very important or the environment is complex, customers should provide design drawings and detailed parameters as much as possible for the company’s experts to review and recommend matching products.
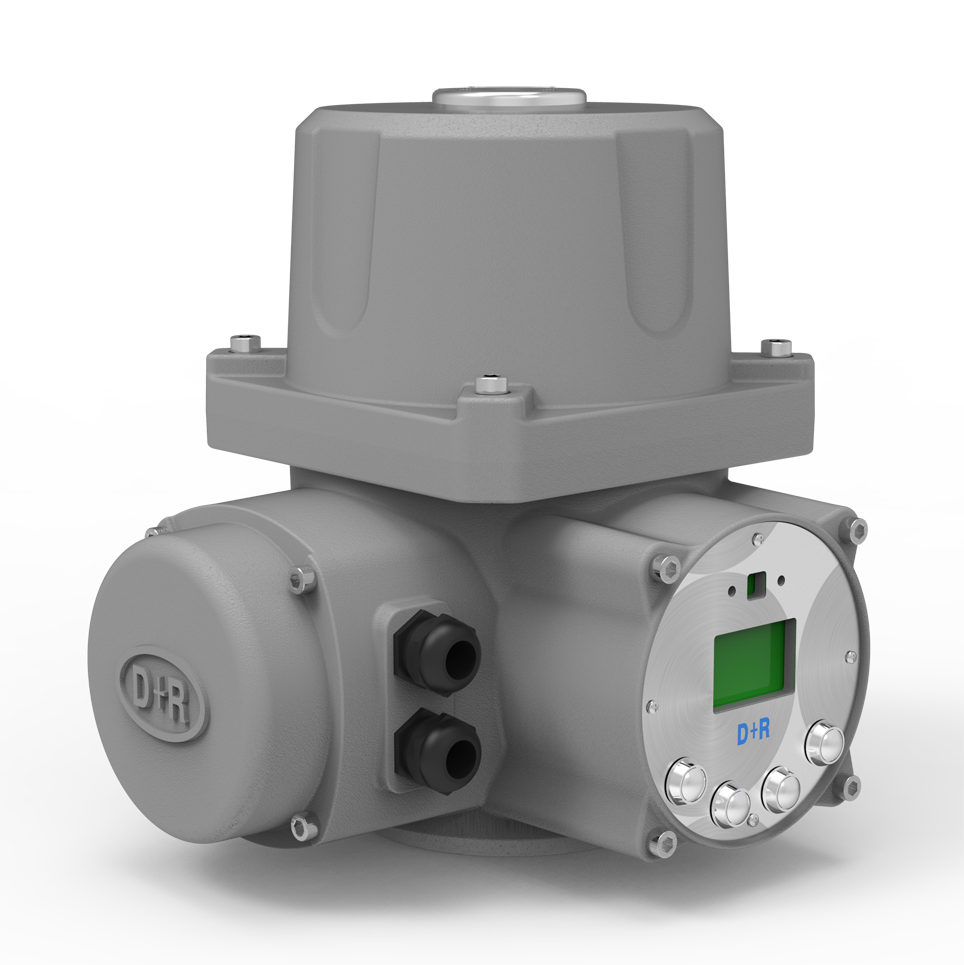